
Journal of Chongqing Jiaotong University (Natural Science) 37(6):98–103+109, DOI: (in Chinese)ĭinnella N, Chiappone S, Guerrieri M (2020) The innovative “NDBA” concrete safety barrier able to withstand two subsequent TB81 crash tests. Science & Technology Review 33(3):54–57, DOI: Ĭui HJ, Xing JK, Li X, Zhu ZQ, Wu WW, Yang HJ (2018) Design and experimental research on movable guardrail of highway central divider. Transportations Research Record 2588(1):116–125, DOI: Ĭui H, Ma X, Li H, Lan T (2015) Simulation of vehicle colliding with steel guardrail based on LS-DYNA. Accident Analysis & Prevention 116:103–115, DOI: īrendan JR Peter TS, Timothy JG (2016) Development of crash modification factors for installation of high-tension cable median barriers. When the wall thickness of the barrier increases by 2 mm, the maximum lateral dynamic deformation was 1,419 mm When the spacing of strengthened columns was reduced to 15 m, the deformation was 1,364 mm After optimization, the deformation was reduced by more than 20%, and the crashworthiness of barrier was improved obviously.Ītahan AO, Hiekmann JM, Himpe J, Marra J (2017) Development of a continuous motorcycle protection barrier system using computer simulation and full-scale crash testing. The simulation results show that the maximum lateral dynamic deformation of the barrier was 1,818 mm, which agrees with the actual vehicle test results (1,600 mm). Finally, the wall thickness and column spacing were optimized according to the results. Secondly, the collision force model was used to calculate the collision of a 10-ton truck, and a finite element model of a typical movable barrier was established for a collision simulation.
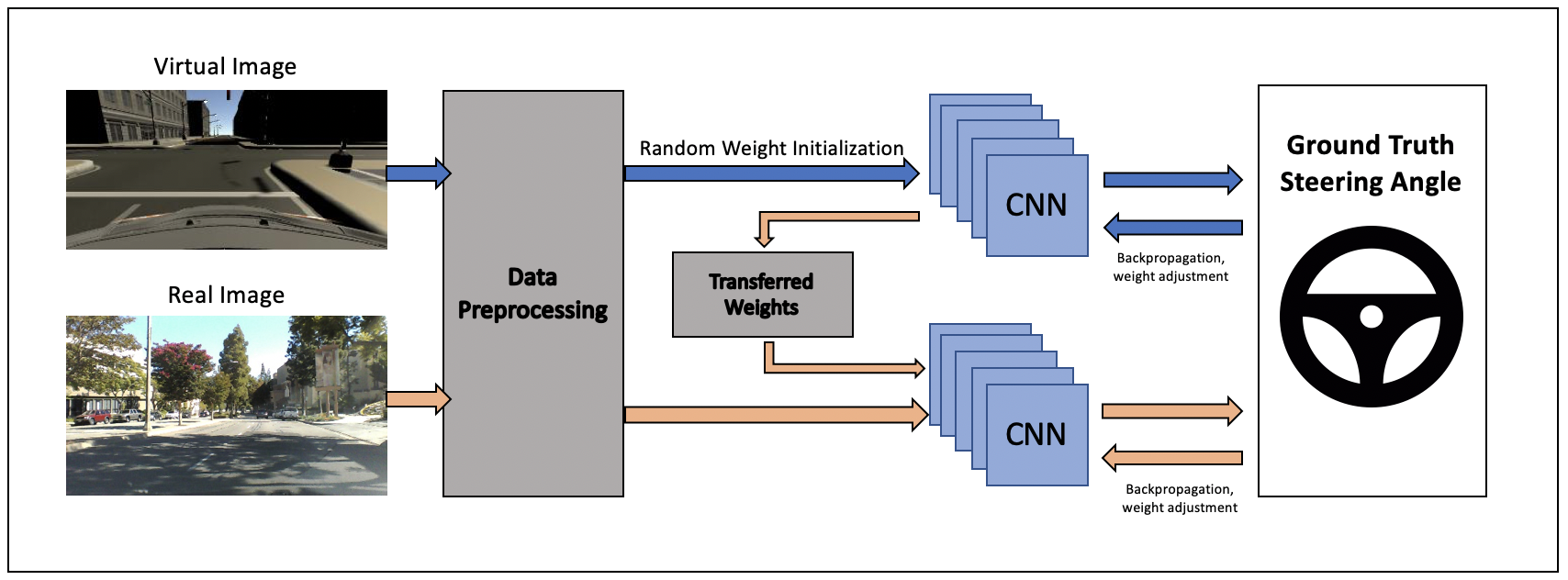
Firstly, the vehicle-barrier mechanical model was established to calculate the vehicle collision force on the barrier. It’s of great significance for improving the crashworthiness of this type of guardrail and enhancing its safety performance. the simulation of multiple impact configurations as the ADAS features vary.To better evaluate the crash performance of the guardrail and reduce the number of actual vehicle crash tests, this paper uses mechanical analysis and finite element simulation technology to evaluate the typical movable guardrail and optimize the structure. These resources savings also imply the possibility to simulate activation of Advanced Driving Assistance Systems (ADAS), i.e.

Therefore, the described model simulation times are evidently shortened in respect to more complicated solution approaches, like FEM or Multi-Body models. Furthermore, real-world crashes and results of the developed model simulations are compared for four different exemplary cases, highlighting the possibility to fully describe the events dynamics and the vehicles deformations. Based on the obtained stiffness value, performed simulations demonstrate the applicability of the method to real vehicle-to-vehicle impacts contained in databases like AREC, VERSUE, etc. However, the different stiffness of the various vehicle areas involves a calibration of the model, using real vehicle-to-barrier crash tests as a reference (carried out by EuroNCAP, NHTSA, etc.). The Finite Element Method (FEM) represents the basis for the analytical formulation of the problem. The paper describes a special purpose 2D vehicle model for time-efficient crash stage simulation and therefore introduces the equations which rule over the model first. The reasons are an increase in the requested vehicles performances in terms of passive and active safety but also the necessity to investigate causes which lead to car accidents. Simulation of vehicle impact stages is gaining more importance as the years go by.
